Gearing
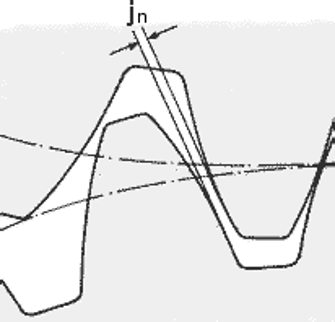
Flank clearance
rothe erde® slewing bearings are mainly designed with spur gears. The gearing carved into one of the bearing rings has the advantage of not needing additional sprockets, thus, reducing construction effort and costs.
For heavily-loaded gear pairings, an addendum flank retraction and a rounding of the head edges is necessary. Bearings with corrected gearing are preferably provided with addendum modification coefficient x = 0.5, see DIN 3994, 3995.
Hardened gearing has been proven to be effective for gears with higher demands on the flanks. Depending on the module and ring diameter, the annular gears are treated both by circulation procedures and by means of inductive single tooth hardening, then mainly as tooth base hardening, Both procedures result in high tooth root strength alongside improved flank carrying capacity. Flank hardening with hardness outlet in the root radius area decreases the root carrying capacity For the hardened gears, an individualised calculation must be carried out.
To check the mesh conditions, the pinion features are to be submitted. During the assembly of the slewing bearing and its accompanying pinion, it must be ensured that there is sufficient tooth flank clearance.
It must be ensured that the tooth flank clearance is set at least at 0.03 module on the three teeth marked in green.
After the final assembly of the machine, and after all the slewing rings’ bolts have been tightened, the flank clearance is to be checked with an appropriate feeler gauge or a lead wire.