Lagerinspektion und Verschleißmessung
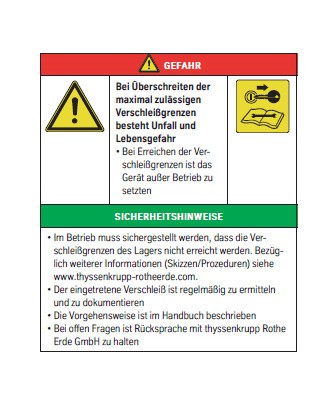
Sicherheitshinweis Verschleißgrenzen
Messung des Kippspiels
Messung des Kippspiels
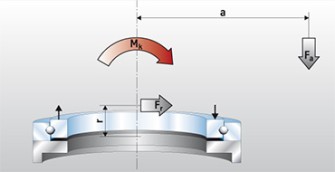
Bild 1: Belastungsprinzip der Kippspielmessung (Axialbewegung)
Wenn möglich, empfehlen wir zur Verschleißbestimmung die Messung des Kippspiels. Das Belastungsprinzip für eine solche Messung zeigt Bild 1.
Es wird zwischen der unteren Anschlusskonstruktion und dem mit der Oberkonstruktion verschraubten Lagerring (Bild 2) gemessen. Um dabei den Einfluss von elastischen Verformungen der Anschlusskonstruktion zu minimieren, muss die Messung möglichst nahe am Laufsystem des Lager stattfinden.
Lagerinspektion - Schäden vorbeugen
Verschleißmessungen ermöglichen eine Früherkennung von technischen Problemen, bevor diese zu ungeplanten Anlagenstillständen führen. So werden unnötige Instandsetzungskosten und teure Produktionsausfälle vermieden. Zur Bewertung des Lagerzustandes empfehlen wir daher regelmäßige Lagerverschleißmessungen.
Der Verschleiß des Laufsystems macht sich durch eine Veränderung der Axialbewegung oder Absenkung bemerkbar. Diese Verschleißerhöhung kann je nach Anwendungsfall oder Lagerausführung durch die Messung des Kippspiels oder durch Absenkmessungen ermittelt werden.
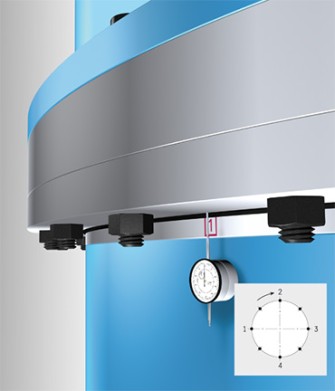
Bild 1: Belastungsprinzip der Kippspielmessung (Axialbewegung)
Ausführung des Verfahrens
- Bei Inbetriebnahme wird eine Referenzmessung durchgeführt.
- Von einer festgelegten Position aus werden die Messpunkte am Umfang markiert.
- Für die Null-Einstellung der Messuhren, die eine Messgenauigkeit von 0,01mm aufweisen sollten, ist zunächst das maximale rückdrehende Moment aufzubringen. Anschließend ist – ggf. durch Lastaufnahme – ein nach vorne kippendes Moment zu erzeugen.
- Nach dem Schwenken der Oberkonstruktion wird die Messung in den markierten Messpositionen wiederholt (siehe Tabelle 4).
Maximal zulässige Vergrößerung der Lagerspiele (gleichmäßiger Verschleiß)
Wichtig: Für besondere Anwendungsfälle (Rücksprache thyssenkrupp rothe erde) sind diese Lagerspielvergrößerungen nicht zulässig. Das betrifft zum Beispiel Großwälzlager für Fahrgeschäfte 50% der aufgeführten Werte.
Tabelle 1: BF* 01, 08 (zweireihiges Kugellager/Axialkugellager)
Messverfahren | Kugeldurchmesser (mm) | ||||||||||
---|---|---|---|---|---|---|---|---|---|---|---|
18 | 20 | 22 | 25 | 30 | 35 | 40 | 45 | 50 | 60 | 70 | |
max. zulässige Verschleißwerte bis mm | |||||||||||
Absenkmessung | 1,6 | 2,2 | 3,0 | 3,8 | |||||||
Kippspielmessung | 2,5 | 3,0 | 4,0 | 5,0 |
Tabelle 2: BF* 06, 09, 25, 23, 28 (Kugellager/Profillager)
Messverfahren | Kugeldurchmesser (mm) | ||||||||||
---|---|---|---|---|---|---|---|---|---|---|---|
20 | 22 | 25 | 30 | 35 | 40 | 45 | 50 | 60 | 70 | ||
max. zulässige Verschleißwerte bis mm | |||||||||||
Absenkmessung | 1,6 | 2,0 | 2,6 | 3,3 | |||||||
Kippspielmessung | 2,0 | 2,6 | 3,2 | 4,0 |
Tabelle 3: BF* 12, 13, 19 (Rollendrehverbindung)
Messverfahren | Kugeldurchmesser (mm) | |||||||||||||
---|---|---|---|---|---|---|---|---|---|---|---|---|---|---|
16 | 20 | 25 | 28 | 32 | 36 | 40 | 45 | 50 | 60 | 70 | 80 | 90 | 100 | |
max. zulässige Verschleißwerte bis mm | ||||||||||||||
Absenkmessung | 0,8 | 1,2 | 1,6 | 2,0 | 2,4 | |||||||||
Kippspielmessung | 1,4 | 2,0 | 2,8 | 3,5 | 4,2 |
Tabelle 1: BF* 01, 08 (zweireihiges Kugellager/Axialkugellager)
Messverfahren | Kugeldurchmesser (mm) | ||||||||||
---|---|---|---|---|---|---|---|---|---|---|---|
18 | 20 | 22 | 25 | 30 | 35 | 40 | 45 | 50 | 60 | 70 | |
max. zulässige Verschleißwerte bis mm | |||||||||||
Absenkmessung | 1,6 | 2,2 | 3,0 | 3,8 | |||||||
Kippspielmessung | 2,5 | 3,0 | 4,0 | 5,0 |
Tabelle 1: BF* 01, 08 (zweireihiges Kugellager/Axialkugellager)
Messverfahren | Kugeldurchmesser (mm) | ||||||||||
---|---|---|---|---|---|---|---|---|---|---|---|
18 | 20 | 22 | 25 | 30 | 35 | 40 | 45 | 50 | 60 | 70 | |
max. zulässige Verschleißwerte bis mm | |||||||||||
Absenkmessung | 1,6 | 2,2 | 3,0 | 3,8 | |||||||
Kippspielmessung | 2,5 | 3,0 | 4,0 | 5,0 |
Tabelle 2: BF* 06, 09, 25, 23, 28 (Kugellager/Profillager)
Messverfahren | Kugeldurchmesser (mm) | ||||||||||
---|---|---|---|---|---|---|---|---|---|---|---|
20 | 22 | 25 | 30 | 35 | 40 | 45 | 50 | 60 | 70 | ||
max. zulässige Verschleißwerte bis mm | |||||||||||
Absenkmessung | 1,6 | 2,2 | 2,6 | 3,3 | |||||||
Kippspielmessung | 2,0 | 2,6 | 3,2 | 4,0 |
Tabelle 2: BF* 06, 09, 25, 23, 28 (Kugellager/Profillager)
Messverfahren | Kugeldurchmesser (mm) | ||||||||||
---|---|---|---|---|---|---|---|---|---|---|---|
20 | 22 | 25 | 30 | 35 | 40 | 45 | 50 | 60 | 70 | ||
max. zulässige Verschleißwerte bis mm | |||||||||||
Absenkmessung | 1,6 | 2,2 | 2,6 | 3,3 | |||||||
Kippspielmessung | 2,0 | 2,6 | 3,2 | 4,0 |
Tabelle 3: BF* 12, 13, 19 (Rollendrehverbindung)
Messverfahren | Kugeldurchmesser (mm) | |||||||||||||
---|---|---|---|---|---|---|---|---|---|---|---|---|---|---|
16 | 20 | 25 | 28 | 32 | 36 | 40 | 45 | 50 | 60 | 70 | 80 | 90 | 100 | |
max. zulässige Verschleißwerte bis mm | ||||||||||||||
Absenkmessung | 0,8 | 1,2 | 1,6 | 2,0 | 2,4 | |||||||||
Kippspielmessung | 1,4 | 2,0 | 2,8 | 3,5 | 4,2 |
Tabelle 3: BF* 12, 13, 19 (Rollendrehverbindung)
Messverfahren | Kugeldurchmesser (mm) | |||||||||||||
---|---|---|---|---|---|---|---|---|---|---|---|---|---|---|
16 | 20 | 25 | 28 | 32 | 36 | 40 | 45 | 50 | 60 | 70 | 80 | 90 | 100 | |
max. zulässige Verschleißwerte bis mm | ||||||||||||||
Absenkmessung | 0,8 | 1,2 | 1,6 | 2,0 | 2,4 | |||||||||
Kippspielmessung | 1,4 | 2,0 | 2,8 | 3,5 | 4,2 |
Überprüfung der Verzahnung
Überprüfung der Verzahnung
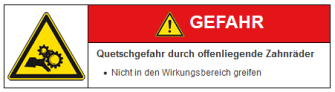
Sicherheitshinweis Quetschgefahr
Im Laufe der Gebrauchsdauer treten Einlaufglättung und Verzahnungsverschleiß auf. Ein zulässiger Verschleißgrenzwert ist stark vom Einsatzfall abhängig. Erfahrungsgemäß kann der zulässige Verschleiß bis zu 0,1 x Modul pro Zahnflanke betragen.
Absenkmessung
Absenkmessung
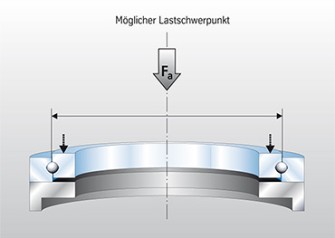
Bild 3: Belastungsprinzip der Absenkmessung
Wo die Messung des Kippspiels nicht möglich ist, empfehlen wir die Absenkmessung. Dabei liegt der Schwerpunkt aus den Lastkombinationen innerhalb des Laufkreisdurchmessers des Lagers. Das Belastungsprinzip ist in Bild 3 dargestellt.
Gemessen wird zwischen der unteren Anschlusskonstruktion und dem mit der Oberkonstruktion verschraubten Lagerring (Bilder 4, 5).
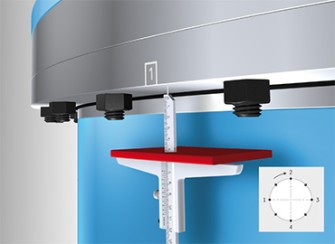
Bild 4: Prinzipieller Aufbau der Absenkmessung mit Tiefenmessschieber
Der Ablauf ähnelt dem bei der Messung des Kippspiels:
- Bei der Inbetriebnahme des Gerätes werden Referenzwerte ermittelt.
- Von einer festgelegten Position aus werden die Messpunkte am Umfang markiert.
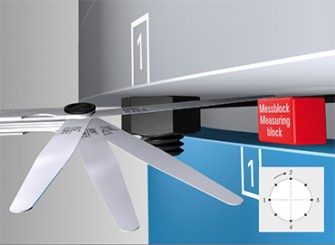
Bild 5: Prinzipieller Aufbau der Absenkmessung mit Fühlerlehre
In geeigneten Zeitabständen sollte nach Überprüfung der Lagerbefestigungsschrauben eine Wiederholung der Kippspiel- oder Absenkmessung unter gleichen Bedingungen durchgeführt werden. Die jeweilige Differenz zur Referenzmessung gibt den zwischenzeitlich eingetretenen Verschleiß an. Bei ansteigenden Verschleißwerten sollte in kürzeren Abständen gemessen werden.
Vorteil: Durch die eindeutige Bewertung des Lagerzustandes können verschlissene Teile rechtzeitig ausgetauscht werden. Zusammen mit einem optimalen Ersatzteil-Management können daher Schadensfälle und längere Stillstandszeiten vermieden werden.
Hinweis: Werden die zulässigen Verschleißwerte überschritten, empfehlen wir eine Stilllegung des Gerätes.
Die Alternative: Integrierte Verschleiß-Messeinrichtung (IWM)
Um die Funktionalität und Betriebssicherheit der Anlagen weiter zu optimieren, arbeitet thyssenkrupp rothe erde unablässig an innovativen Lösungen für die permanente Zustandsüberwachung. Die integrierte Verschleiß-Messeinrichtung für Großwälzlager ist eine patentierte Erfindung. Sie ermöglicht eine Online-Überprüfung des maximal zulässigen Axialspiels beziehungsweise der Absenkung der Drehverbindung.
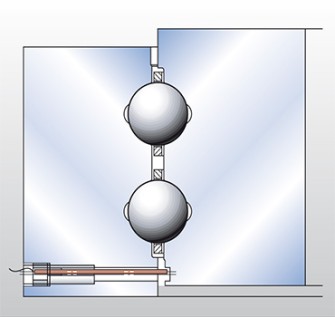
Bild 6: Verschleißmessung in einem Kugellager
Vorteil: Betriebsunterbrechungen zur Erfassung des Axialspiels sind nicht notwendig.
Im Bereich der Scheitellast der Laufbahnen befindet sich ein Stift aus nicht rostendem Stahl. Dieser ist – elektrisch isoliert – in einen Ring montiert. Der Stift ragt in eine Nut, die sich im Gegenring befindet. Das maximal zulässige Spiel ist über die Nutbreite einstellbar.
Ändert sich das Spiel unzulässig stark, geraten Ring und Stift in Kontakt. Durch die elektrische Verbindung des Stiftes wird bei der Berührung von Stift und Gegenring ein Signal ausgelöst. Dieses Signal zeigt an, dass die zulässige Relativ-Verschiebung der Ringe erreicht und eine Lagerprüfung notwendig ist.
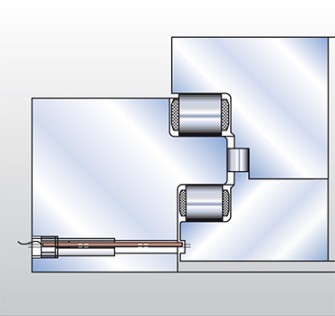
Bild 7: Verschleißmessung in einem Rollenlager
Vorteil: Die Verformung der Anschlusskonstruktion oder Elastizitäten der Schraubverbindungen beeinflussen das Messergebnis nicht wesentlich.
Die elastische Annäherung der Laufbahnen, das Axialspiel des Lagers und die Ebenheitsabweichung der Auflagefläche werden kompensiert. Kosten für das Wartungspersonal werden minimiert.
Fettprobenentnahme
Fettprobenentnahme
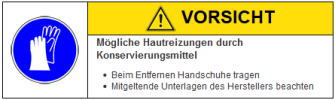
Warnhinweis für mögliche Hautreizungen durch Konservierungsmittel
Fettprobenentnahmeset
Fettprobenentnahmeset
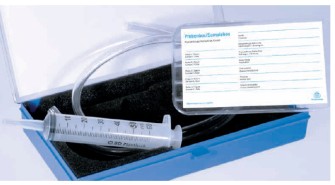
Bild 8: Fettprobenentnahmeset
Zeitgleich zu den Inspektionsmessungen werden Gebrauchtfettproben entnommen. Die Gebrauchtfettanalyse ergibt weitere Information über den Laufbahnzustand.
Lager mit Fettentnahmebohrungen
Lager mit Fettentnahmebohrungen
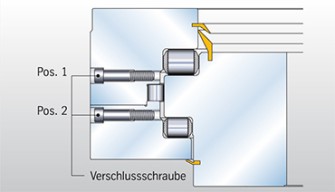
Bild 9: Dreireihige Rollendrehverbindung mit Fettentnahmebohrungen
Das Fettproben-Entnahme-Set besteht aus einem Plastikschlauch, diversen Verschlusskappen, einer Saugvorrichtung und einer Probenbox für maximal fünf Fettproben sowie einem Info-Blatt. Die Vorgehensweise wird detailliert beschrieben.
Die Fettproben müssen aus der Hauptbelastungszone entnommen werden.
Die für die Probenentnahme ausgewählte Verschlussschraube (M16 EN ISO 4762) wird entfernt (Bilder 9 und 10: Position 1 und gegebenenfalls gegenüber, Position 2).
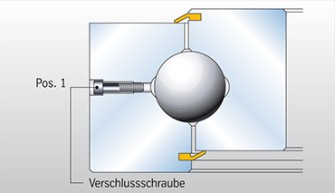
Bild 10: Einreihiges Kugellager mit Fettentnahmebohrung
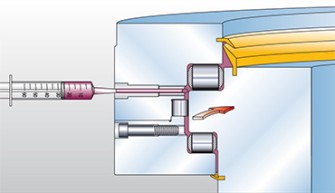
Bild 11: Entnahme
Vor Entnahme der Fettprobe ist der mitgelieferte Schlauch, geringfügig länger als die Gesamtlänge der Fettentnahmebohrung, schräg (45°) abzuschneiden. Der Schlauch wird bis in den Laufbahnbereich in die entsprechende Bohrung eingeführt (Bild 11).
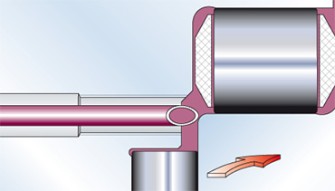
Bild 12: Detailausschnitt Entnahme
Dabei muss die 45°-Schnittfläche entgegen der Drehrichtung positioniert werden (Bild 12).
Die Entnahmebohrungen sind mit den Verschlussschrauben wieder zu verschließen.
Nach der Fettentnahme werden beide Schlauchenden mit den Plastikkappen verschlossen.
Die Fettprobe wird nummeriert und in die gekennzeichnete Probenbox abgelegt.
Die Probenbox wird mit den notwendigen Informationen (siehe Fettprobenentnahmeset, Bild 8) auf der Oberseite versehen.
Lager ohne Fettentnahmebohrungen
Lager ohne Fettentnahmebohrungen
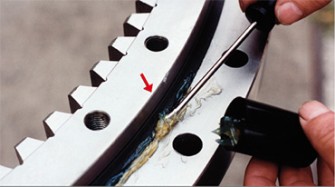
Bild 13: Fettentnahme an der Dichtlippe
Wenn keine Fettentnahmebohrungen am Lager vorgesehen sind, werden eine oder mehrere Fettproben an der Dichtung entnommen. Dieser Bereich wird in Nähe eines Schmiernippels gereinigt. Bevorzugt sollte die Entnahme im Hauptarbeitsbereich und/oder 180° versetzt, erfolgen.
Während der Nachschmierung an dem oben genannten Schmiernippel (ohne Drehung des Lagers) wird das erste austretende Fett an der Dichtlippe entnommen (Bild 13). Eine Menge von 3 ccm ist ausreichend.
Hinweis: Achten Sie bitte auf eine sorgfältige Entnahme, ansonsten erhalten Sie eine Ergebnisverfälschung durch Verunreinigung.
Fe-Grenzwerte
Fe-Grenzwerte
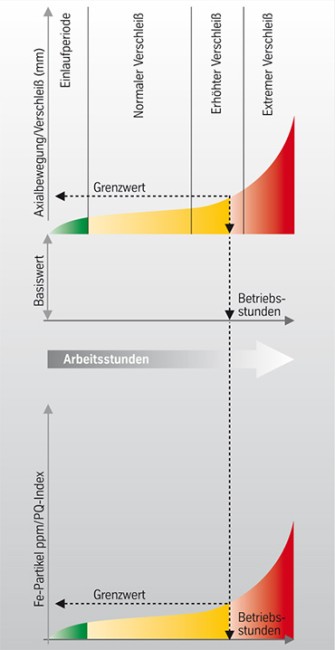
Bild 14: Verschleißkurven
Ein Grenzwert für zulässige Fe-Kontaminierung des Schmierstoffs ist im starken Maß von den Betriebsparametern und Nachschmierintervallen abhängig. Je nach Einsatzfall kann der Wert bis zu 20.000 ppm betragen.
Verschleißkurven
Das Diagramm zeigt die Verschleißzunahme, beziehungsweise Fe-Partikel- und PQ-Index-Zunahme in Abhängigkeit von den Betriebsstundenzahlen (Bild 14).
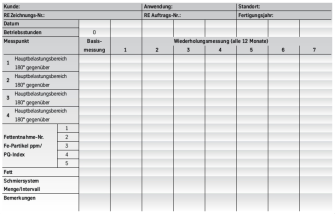
Tabelle 4: Messtabelle
zum Vergrößern hier klicken
Für Standardanwendungsfälle siehe Werte in den Tabellen 1 - 3. Bei Erreichen der Grenzwerte bitte Rothe Erde kontaktieren.
Die Mess- und Analysewerte sowie die lagerspezifischen Infomationen sollten in eine separate Tabelle (siehe Tabelle 4) eingetragen und Rothe Erde zur Verfügung gestellt werden. Die Probenbox bitte an Rothe Erde senden.
thyssenkrupp rothe erde Germany GmbH
Service
Beckumer Straße 87
59555 Lippstadt
service.rotheerde@thyssenkrupp.com
Rothe Erde sendet die Fettproben an ein geprüftes und qualifiziertes Labor.
Vorteil: Kurze Bearbeitungszeit und Informationsaufgabe per E-Mail zu dem Analyseergebnis sowie der Verschleißmessung.
Fordern Sie das Fettprobenentnahmeset unter folgender Adresse an:
thyssenkrupp rothe erde Germany GmbH
Tremoniastraße 5–11
44137 Dortmund
Telefon (02 31) 186-0
Telefax (02 31) 186-2500
sales.rotheerde@thyssenkrupp.com